Enhancing Production Processes: How Digital Twins Revolutionize Manufacturing
In an era of rapid technological advancements, digital twins have emerged as a game-changer in the manufacturing industry. By creating virtual replicas of physical assets, processes, and systems, digital twins enable manufacturers to optimize their operations, enhance productivity, and drive innovation. In this article, we will explore the importance of digital twins in manufacturing and how they revolutionize production processes.
Streamlining Design and Development
One of the key advantages of digital twins in manufacturing is their ability to streamline design and development processes. By creating a virtual replica of a product or system, manufacturers can identify potential issues or bottlenecks early on in the design phase. This allows them to make necessary modifications and improvements before physical production begins.
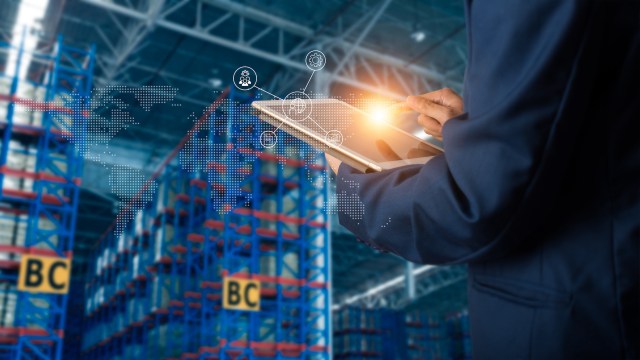
Digital twins also enable manufacturers to conduct simulations and tests virtually, reducing the need for costly physical prototypes. With real-time data integration, designers can analyze performance metrics and make data-driven decisions to optimize designs further. This not only saves time but also improves overall product quality.
Improving Operational Efficiency
Digital twins play a vital role in improving operational efficiency within manufacturing facilities. By monitoring real-time data from sensors embedded in physical assets, manufacturers gain valuable insights into their performance metrics. These insights can be used to identify inefficiencies, predict maintenance needs, and optimize operational processes.
For example, if a machine within a production line starts showing signs of wear or decreased efficiency based on data collected by its digital twin, maintenance teams can be alerted proactively. This allows them to address the issue before it leads to unexpected downtime or costly breakdowns.
Furthermore, by leveraging predictive analytics capabilities offered by digital twins, manufacturers can optimize production schedules based on demand forecasts. This ensures that resources are allocated efficiently and production targets are met without unnecessary delays or overproduction.
Enhancing Product Lifecycle Management
Digital twins facilitate enhanced product lifecycle management across various stages – from design to disposal. By continuously monitoring the performance of physical assets through their digital counterparts, manufacturers can gather valuable data on usage patterns, environmental conditions, and maintenance history.
This data-driven approach enables manufacturers to make informed decisions regarding product improvements, upgrades, or even new product development. By understanding how products are used and how they perform over time, manufacturers can identify opportunities for innovation and tailor their offerings to meet customer demands better.
Digital twins also play a crucial role in warranty management and after-sales support. With real-time access to product performance data, manufacturers can proactively identify potential issues and provide timely support or service to customers. This not only enhances customer satisfaction but also strengthens brand reputation.
Enabling Continuous Improvement
The use of digital twins in manufacturing enables continuous improvement by providing a feedback loop for iterative enhancements. By capturing real-time data from physical assets and processes, manufacturers can analyze performance trends and identify areas for optimization.
With the insights gained from digital twins, manufacturers can implement changes that drive process efficiencies, reduce waste, improve quality control measures, and enhance overall productivity. This iterative approach ensures that manufacturing processes are continually evolving to meet changing market demands and technological advancements.
In conclusion, digital twins have become an indispensable tool in revolutionizing manufacturing processes. From streamlining design and development to improving operational efficiency and enabling continuous improvement, digital twins offer numerous benefits for manufacturers. Embracing this technology allows businesses to stay ahead of the competition by optimizing their operations, enhancing product quality, and driving innovation in the ever-evolving manufacturing landscape.
This text was generated using a large language model, and select text has been reviewed and moderated for purposes such as readability.